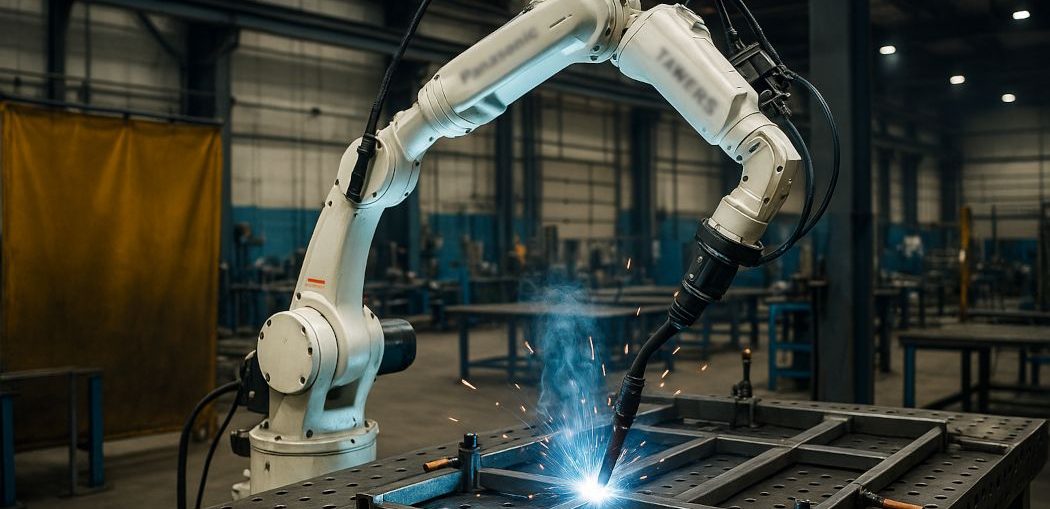
Współczesne technologie spawania zrobotyzowanego zrewolucjonizowały przemysł wytwórczy, oferując bezprecedensową precyzję, powtarzalność i wydajność. Zaawansowane systemy spawalnicze integrują szereg wyspecjalizowanych komponentów, których synergiczne działanie umożliwia realizację złożonych procesów produkcyjnych. W artykule przedstawiamy szczegółową charakterystykę poszczególnych elementów składowych nowoczesnych stanowisk spawalniczych, ich funkcjonalności oraz wzajemne powiązania technologiczne.
1. Jednostki robotyczne w procesach spawalniczych
1.1. Rodzaje manipulatorów przemysłowych
W zautomatyzowanym spawalnictwie dominują rozwiązania oparte na:
- Robotach sześcioosiowych o strukturze szeregowej
- Manipulatorach kolaboratywnych (coboty) do pracy w bliskiej obecności operatorów
- Systemach portalowych do obsługi dużych powierzchni
- Zespołach robotów współpracujących przy kompleksowych zadaniach
1.2. Specyfikacja techniczna
Podstawowe parametry robotów spawalniczych obejmują:
- Precyzja pozycjonowania: od ±0,02 mm dla aplikacji precyzyjnych
- Przestrzeń robocza: od 0,5 m³ do ponad 50 m³ w systemach wielorobotowych
- Dynamiczna stabilność: systemy tłumienia drgań podczas szybkich manewrów
- Odporność środowiskowa: klasy IP67 dla trudnych warunków produkcyjnych
1.3. Innowacyjne rozwiązania konstrukcyjne
Nowoczesne manipulatory spawalnicze wyposaża się w:
- Zintegrowane systemy chłodzenia wodnego
- Moduły wymiany narzędzi w czasie poniżej 0,5 sekundy
- Systemy samodiagnostyki stanu mechanicznego
- Aktywne układy kompensacji odkształceń termicznych
2. Technologie łączenia materiałów
2.1. Zautomatyzowane głowice spawalnicze
2.1.1. Głowice łukowe
- Systemy MIG/MAG z adaptacyjną kontrolą parametrów
- Zaawansowane rozwiązania TIG z precyzyjnym podawaniem drutu
- Hybrydowe systemy laserowo-łukowe
2.1.2. Technologie bezłukowe
- Spawanie laserowe z systemami śledzenia wiązki
- Zgrzewanie oporowe z kontrolą siły docisku
- Spawanie elektronowe w komorach próżniowych
2.2. Zaawansowane systemy podawania
Nowoczesne rozwiązania w zakresie podawania materiału:
- Inteligentne podajniki z funkcją predykcji zacięć
- Systemy wielomateriałowe do aplikacji specjalnych
- Automatyczne stacje przygotowania drutu (prostowanie, czyszczenie)
- Moduły dozowania topników i past lutowniczych
3. Inteligentne systemy sterowania
3.1. Architektura kontroli procesu
Współczesne systemy sterowania oferują:
- Zintegrowane środowiska programistyczne
- Cyfrowe bliźniaki procesów technologicznych
- Algorytmy samouczące się optymalizujące parametry
- Rozproszone systemy akwizycji danych
3.2. Metody programowania
Ewolucja technik programowania obejmuje:
- Generowanie kodu na podstawie modeli CAD/CAM
- Systemy rozpoznawania gestów operatora
- Programowanie przez demonstrację (PbD)
- Chmurowe platformy współdzielenia programów
4. Zaawansowane systemy pomocnicze
4.1. Technologie pozycjonowania
Innowacyjne rozwiązania w zakresie manipulacji detalem:
- Adaptacyjne systemy mocowania z czujnikiem siły
- Roboty współpracujące w roli pozycjonerów
- Magnetyczne systemy mocowania dla dużych konstrukcji
- Wirtualne pozycjonery w systemach rozszerzonej rzeczywistości
4.2. Systemy zapewnienia jakości
Kompleksowe podejście do kontroli jakości:
- Wbudowane systemy tomografii akustycznej
- Spektrometryczne analizy składu chemicznego w czasie rzeczywistym
- Systemy wizyjne z algorytmami głębokiego uczenia
- Predykcyjne modele odkształceń termicznych
5. Integracja i bezpieczeństwo
5.1. Systemy współpracy człowiek-maszyna
Nowe standardy bezpieczeństwa obejmują:
- Systemy wykrywania intencji operatora
- Aktywne powierzchnie dotykowe z funkcją wykrywania kontaktu
- Adaptacyjne ograniczenia prędkości w zależności od odległości
- Wirtualne bariery bezpieczeństwa
5.2. Ekosystem przemysłowy
Kompleksowa integracja z infrastrukturą produkcyjną:
- Cyfrowe platformy zarządzania flotą robotów
- Systemy wymiany danych w standardzie OPC UA
- Integracja z łańcuchem dostaw Industry 4.0
- Zdalne centra monitorowania i diagnostyki
Perspektywy rozwojowe
Automatyzacja procesów spawalniczych wkracza w erę inteligentnych systemów autonomicznych, gdzie kluczową rolę odgrywają:
- Algorytmy sztucznej inteligencji do samooptymalizacji procesów
- Roboty mobilne z autonomiczną nawigacją
- Systemy samooczyszczających się głowic spawalniczych
- Kwantowe czujniki procesowe
- Biometryczne interfejsy operatora
Dalszy rozwój technologii spawania zrobotyzowanego będzie koncentrował się na zwiększaniu autonomii systemów, redukcji czasu przezbrojenia oraz pełnej integracji z cyfrowymi ekosystemami produkcyjnymi.